熊本地震發生後,部份在日本生產的零組件面臨斷鏈的危機,其中,豐田汽車(Toyota)的影響甚鉅,自地震發生後,在日本全國有26條生產線停工,可能產生偌大的損失,同時暴露出其供應鏈策略(JIT)的弱點,以下簡單解析,
一、供應鏈策略:準時生產(Just In Time, JIT)
依照MBA LIB智庫的解釋,準時化生產JIT是二戰以後最重要的生產方式之一。由於它起源於日本的豐田汽車公司,因而曾被稱為“豐田生產方式”,後來隨著這種生產方式的獨特性和有效性,被越來越廣泛地認識、研究和應用,人們才稱為JIT。JIT生產方式的基本思想是“只在需要的時候,按需要的量,生產所需的產品”,也就是追求一種無庫存,或庫存達到最小的生產系統。JIT的基本思想是生產的計劃和控制及庫存的管理。
其一,JIT的基礎之一是均衡化生產,即平均製造產品,使物流在各作業之間、生產線之間、工序之間、工廠之間平衡、均衡地流動。為達到均衡化,在JIT中採用月計劃、日計劃,並根據需求變化及時對計划進行調整。其二,JIT強調全面質量管理,目標是消除不合格品。消除可能引起不合格品的根源,並設法解決問題,JIT中還包含許多有利於提高質量的因素,如批量小、零件很快移到下工序、質量問題可以及早發現等。其三,由訂單驅動生產,採用拉貨的方式把供、產、銷緊密地銜接起來,使物資儲備,成本庫存和在製品大為減少,提高了生產效率。

簡言之,以JIT模式生產的Toyota,為了即時生產,往往僅握有數個小時的庫存,亦即極度仰賴供應商的穩定供貨,因此當突發狀況發生時,若出現斷鏈的危機,整條生產線也將會停擺。除了在過去發生的危機,包括1997年豐田因供應商Aisin工廠火災而致停工、2007年旗下的供應商Riken因地震受損而嚴重影響生產進度、2011年日本地震與海嘯損及660個供應商並停工許久,都可以看到災害的影響對於JIT供應策略的打擊甚深。
二、應對策略:不是JIT不好,而是專注在問題的本質比較重要
面對天災人禍所暴露出的風險,豐田自2011年日本大地震後一直在思考,如何在生產效率與風險管理上取得一個平衡,以面對未來更多的偶發性事件。Toyota認為,調高零件的庫存水位是治標不治本的,因為即便將庫存由現今的數小時拉高至2週以上,還是不能有效規避大型天災所帶來的風險,平時更要負擔維持高水位庫存的巨額成本,不僅與JIT的觀念背道而馳,更不符合其企業的經營理念。
Toyota認為必須先理解問題的本質,並快速從危機裡恢復元氣才是最重要的策略。豐田想要分散風險,除了開始將許多零件與不同的供應商採購,還建立完整的廠商資料庫,上至大廠下至小商家都入列,並詳細記錄其生產的物件、生產基地的位置以及供應的對象為何,以利危機發生時能快速應變。而供應商往往為了接到Toyota的訂單,也趨向多樣化、不同基地的生產,以配合豐田轉變的策略。
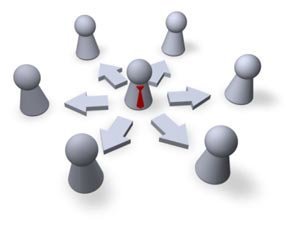
面對這次的震災,專家表示,豐田斷鏈危機並不在於其生產與管理策略出現什麼重大的缺失,而是生產基地建在地震頻繁的日本,因此如何規避天災帶來的風險,的確是豐田要持續省思的課題。
每週500字 商業 邏輯 新聞
更多資訊WSJ
沒有留言:
張貼留言